Boiler Houses
Energy cost reduction through online water quality monitoring
Monitoring the water quality is an important first step in reducing energy costs in any facility that works with hot water and steam boilers.
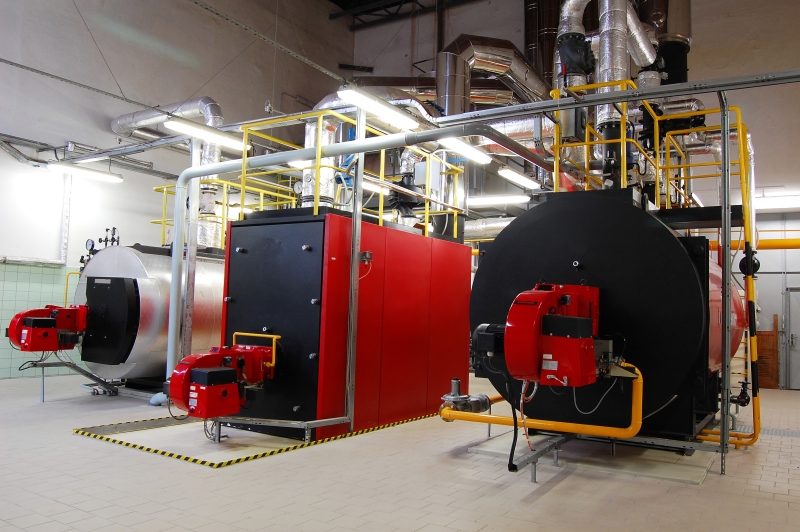
Modern steam boilers benefit from water quality monitoring (© Fotosearch)
Recent surveys have shown that improved control of parameters such as water hardness, carbonate hardness and conductivity by online monitoring can save water quality facilities several thousand euros annually in energy and downtime.
Monitoring the water quality can also significantly increase the service life of a hot water or steam boiler, which in turn leads to major savings in assets and investments.
Virtually any facility that is operated with energy-related heat generation (e.g. hot water or steam boiler plants, as well as open or closed cooling towers) is very susceptible to higher operating costs due to limescale.
How does limescale originate?
The alkaline earth metals found in water (calcium, magnesium) as well as the carbon dioxide bound to the alkaline earth metals dissolve with increasing water temperature. Severe limestone occurs as a result, particularly in hot water systems.
Lime in the chemical sense is calcium carbonate. The carbonic acid, which keeps the salts dissolved, is expelled by the heating of the water – the lime/carbonic acid equilibrium no longer exists. Lime precipitation occurs.
What are the consequences of limescale?
Even the slightest amounts of limescale reduce the heat transfer. This alone is an important factor for increasing energy costs. Severe limescale can even lead to local overheating of the metal resulting in the formation of cracks.
Also aggregates such as pumps are also loaded more. The cross–sectional constrictions of the pipe cause increased flow resistance within the pipe network (the kvs values increase). This leads to increasing energy and follow-up costs.
We would like to give you the following example to illustrate this case:
A limescale coating of 1.0 mm thickness reduces, for example, the heat transfer coefficients of plate heat exchangers or tubular heat exchangers by up to 80%. This leads to a reduction in heat transfer of up to 30%. Even a seemingly insignificant limescale coating of only 1 mm thickness can ultimately lead to a maximum of 12% higher energy costs.
Graphic 1 and 2: Energy loss due to limescale
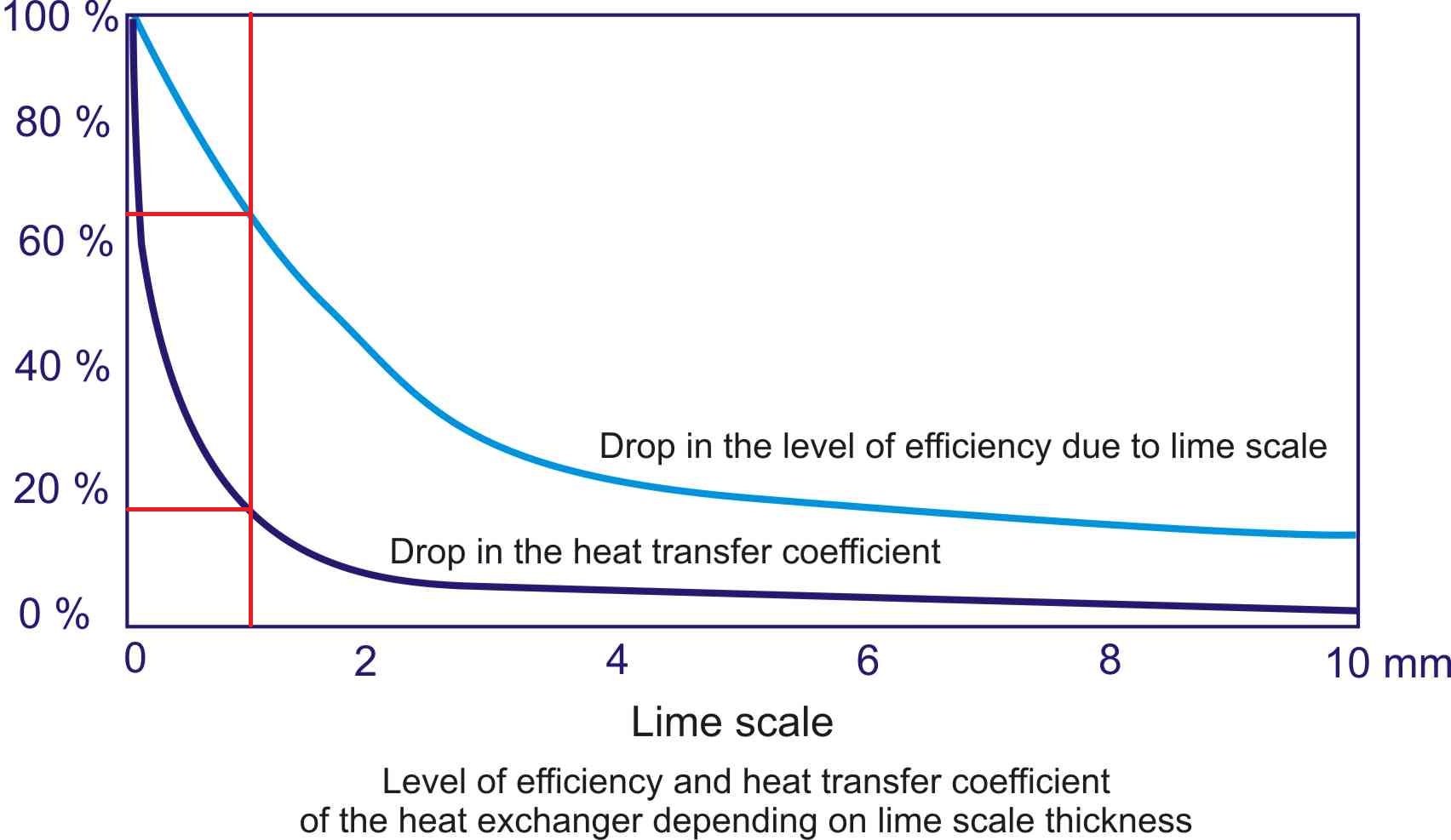
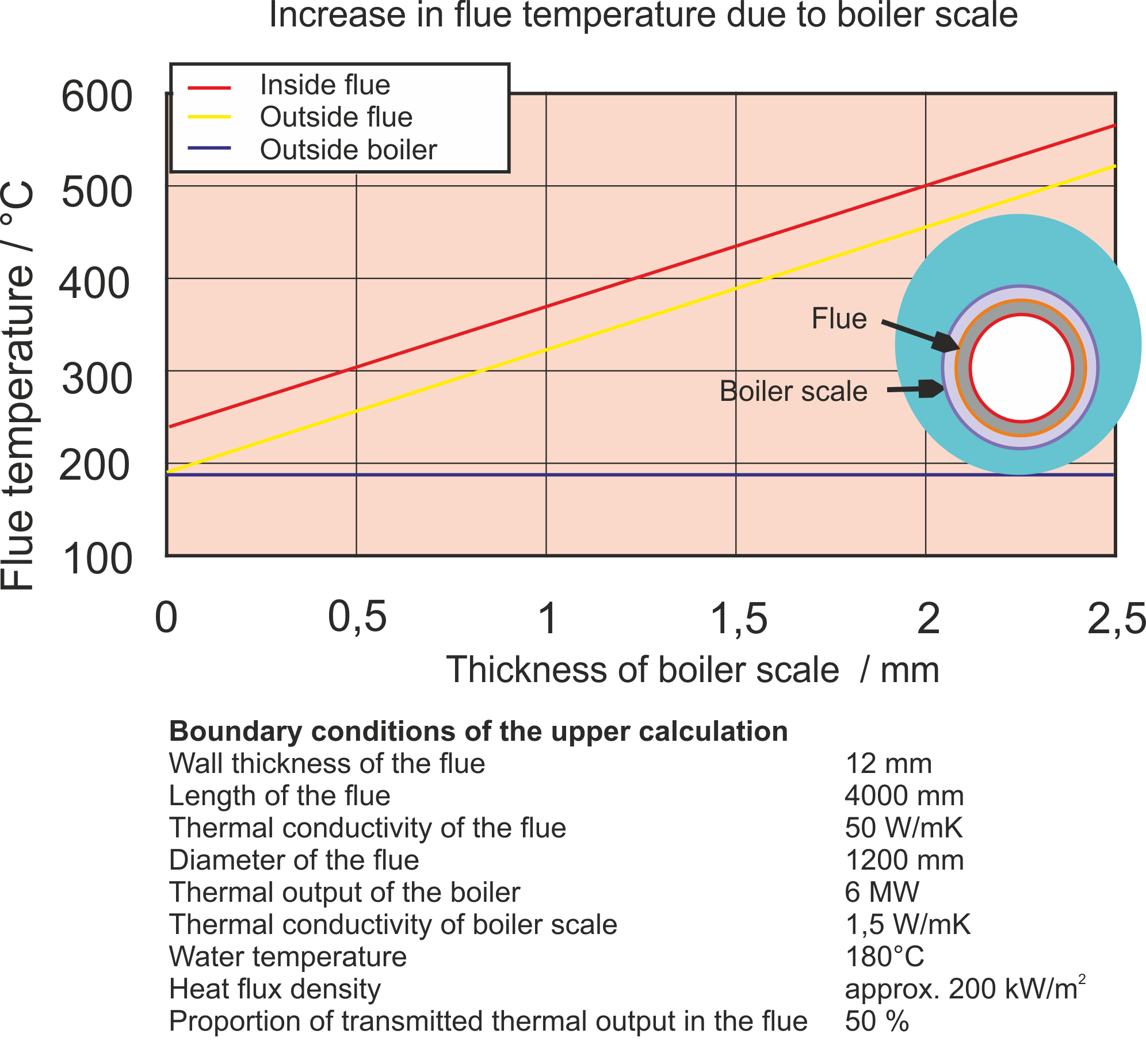
Scale formation in steam boiler plants without monitoring the boiler water and feed water
With the operating parameters listed below and a constant feed water hardness of only 0.1°dH = 1.8 g/m³ CaCO₃, approximately 90 kg of CaCO₃ (lime) is deposited per year over a boiler heating surface of 300 m². A lime coating of approximately 0.12 mm may already form in the first year.
Even this low amount already leads to significant losses in heat transfer and to significant energy losses. This corresponds to about 2% additional energy expenditure in relation to the total energy expenditure.
At a gas or oil price of 4 cents/kWh this corresponds to approximately €3880 per year in additional costs
Example of a 15 t/h steam boiler:
Condensate recovery (45%) | 6,75 m³/h |
Replenishment of feed water (55%) | 8,25 m³/h, [total 49.500 m³ per year] |
Operating hours | 6000 hours per year |
Water hardness | 0,1°dH = 1,8 g/m³ CaCO₃ |
Heating surface | 300 m³ |
Hardness ruptures with higher values lead to significantly increasing energy costs:
Water hardness | Limescale per year | Additional energy expenditure* |
---|---|---|
0,1°dH | 0,11 mm | 20.300 € per year |
0,5°dH | 0,54 mm | 64.300 € per year |
1,0°dH | 1,08 mm | 105.700 € per year |
* with a gas/oil price of 4 cents/kWh
Calculator
Use our calculator to calculate the additional energy costs for your system configuration!
The monitoring of the feed water for hot water and steam boiler plants with the Testomat® EVO TH certified in accordance with the new TÜV standard WÜ 100 for steam boiler plants, prevents this additional energy consumption.
Your content goes here. Edit or remove this text inline or in the module Content settings. You can also style every aspect of this content in the module Design settings and even apply custom CSS to this text in the module Advanced settings.
The purchase of a Testomat® EVO TH pays for itself after only a few months.
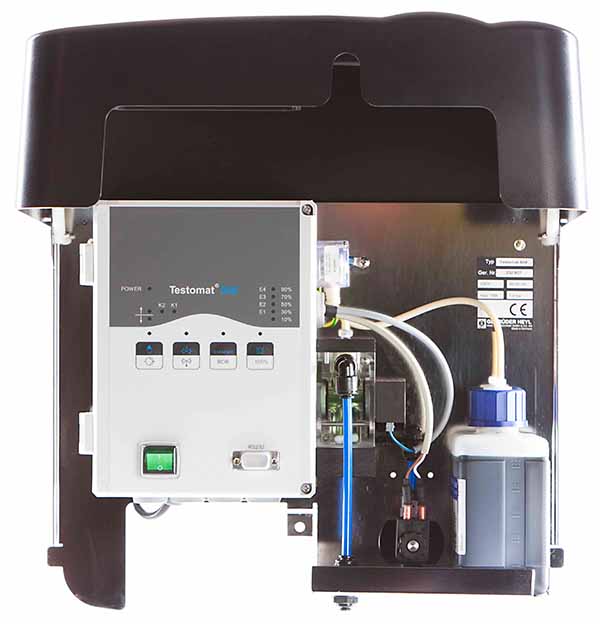
The purchase of a limit device Testomat 808® for small steam generators in accordance with DIN EN 12952-7 pays for itself even faster!
Are there any other effects on the performance of hot water and steam boiler plants?
Water hardness not only results in additional energy costs due to limescale, it can also lead to even more harmful scaling due to a combination of other factors.
Silicates, sulphates and calcium phosphate in the feed water all lead to deposits on the heat exchange surfaces. The existence of an increased amount of any of these substances in the feed water of energy-related heat generators can result in costs of up to €15,000 per year. If, in addition to the lime, deposits are caused by the occurrence of these substances, the costs can be very high due to energy loss, descaling and further potential damage to the boilers and other equipment.
Energy losses due to deposits of calcium carbonate, sulphate and calcium phosphate:
Coating of 1 mm | Energy loss | Oil or gas consumption |
---|---|---|
Calcium carbonate | ∼ 11,0% | 533 m³/a |
Sulphate | ∼ 9,0% | 436 m³/a |
Calcium phosphate | ∼ 4,5% | 218 m³/a |
What are the effects of downtime of the hot water and steam boiler plants on the usual operating costs?
Downtime of plants are an important cost factor and play an important role in the decision in favour of better monitoring of the water quality with an online analysis instrument. Plants or facilities must be switched off for necessary boiler cleaning. This occurs frequently if the water hardness has resulted in increased limescale. Plant operators and plant technicians can reduce these costs significantly by monitoring the water hardness with a Testomat® EVO TH in boiler houses or with a Testomat 808® for small steam generator plants.
Downtime | Frequency | Days per year | Loss of production* |
---|---|---|---|
Without hardness monitoring | About 2-3 times per year | About 8-12 | approx. 10.000 – 70.000 € |
With hardness monitoring | Once per year | About 4 | approx. 5.300 € |
* Based on a 15 t saturated steam boiler for commercial use
-> Our Testomat® EVO TH checks your feed water and condensate water in accordance with the current TÜV WÜ 100 regulation for water hardness in your hot water and steam boiler plants and supports you in maximising the efficiency of your plant.
Are there other factors which are important for the maintenance of hot water and steam boiler plants and should therefore be monitored?
The dissolved salts remain in the water during the generation of steam and increase the concentration of salt in the boiler water.
The increased concentration of salt results in more rapid formation of solid deposits, thus weakening the heat transfer, and can lead to corrosion of the boiler and to foam formation. This foam can be removed with the steam and can adversely affect the downstream plant components.
How can Gebrüder Heyl instruments help you in controlling the quality of your hot water and steam boiler plants?
The Testomat® EVO TH analyses the hardness of the feed water in a quantity or time-controlled manner. If the maximum hardness is exceeded, the Testomat® EVO TH sends a signal to a controller. The controller then controls the filter replacement and triggers the regeneration of the exhausted filter. Both instruments have alarm signal outputs for unforeseen events (e.g. low water pressure, low filter capacity, limit exceeded). They can send these signals at the same time via a 4-20 mA interface to a main control unit or to a central building control system.
Graphic 3: Online-monitoring of water quality with instruments from Gebrüder Heyl
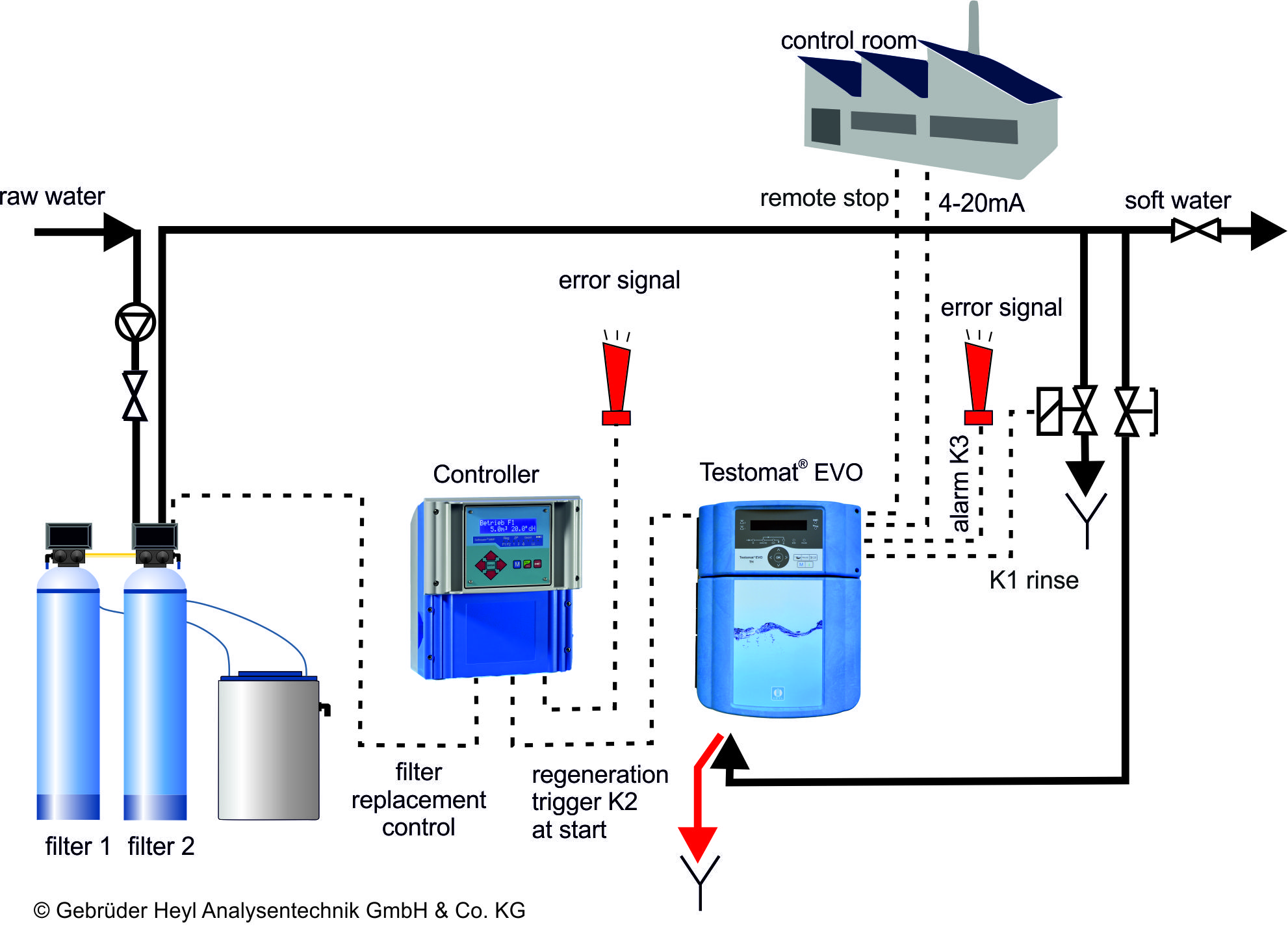
To prevent corrosion due to salt, the conductivity of the feed water is controlled with a monitoring instrument. The controller controls the flushing of boiler water with a high concentration of salt and the supply of water if necessary to maintain the correct salinity.
Graphic 4: Monitoring the boiler water
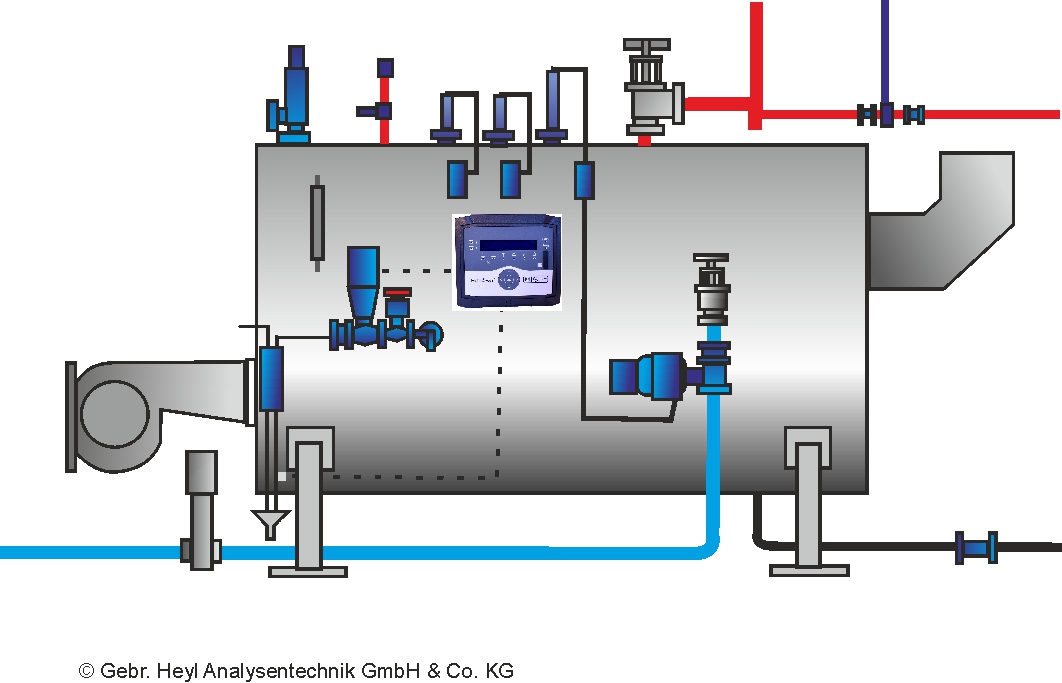
How can the water treatment process be improved by online analysis instruments?
Plant operators and plant technicians can increase the efficiency of the process for softening the boiler water by constant monitoring of the water quality. The water quality monitoring enables operators to detect whether the regeneration process runs correctly, the resin quality is sufficient and whether the regeneration conditioning agents are sufficient and available in the correct consistency.
The combination of Testomat® EVO TH and a controller results in less waste water, lower salt consumption and cost savings due to lower energy requirements.
Which companies can save energy costs by monitoring the water quality with online analysis instruments?
These are, for example, companies which use low pressure boilers:
![]() |
Bakeries |
![]() |
Meat processing firms |
![]() |
Steam generation in food |
![]() |
Laundries |
High pressure boilers are manufactured as high-capacity boilers with a permitted operating pressure of 1 to 25 bar. Companies from the following sectors use this technology:
![]() |
Food and beverage industry (breweries, dairies) |
![]() |
Pulp and paper industry |
![]() |
Chemical industry |
![]() |
Pharmaceutical industry |
![]() |
Building materials industry |
Sources
Verein Deutscher Ingenieure (The Association of German Engineers), directive 2035
© July 2013 Technical information of Gebrüder Heyl Analysentechnik GmbH & Co. KG. Redistribution and reproduction of this document requires our explicit approval. Revised April 2024